ADPO
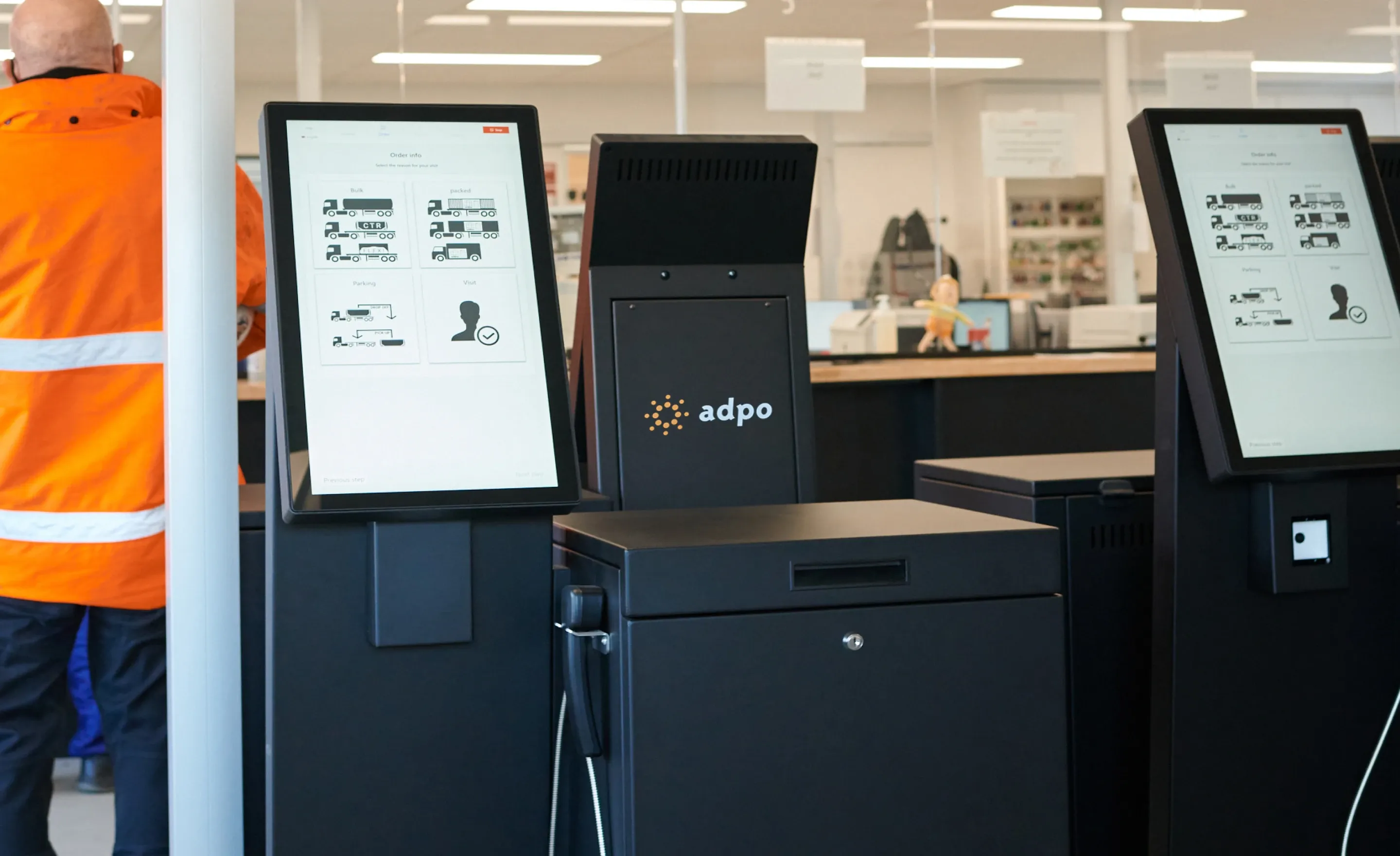
Innovating towards a digital terminal.
Antwerp Distribution & Product Operations – ADPO – is a logistics service provider that offers a comprehensive range of liquid bulk services. Its primary focus is on tank storage, leveraging the world’s largest stainless steel storage facility. In addition, ADPO’s integrated terminal model encompasses warehousing, cleaning, packaging, repairing, full ISO container logistics, transport, and custom services.
These extensive services are conveniently consolidated at a single, exceptional location within the esteemed Port of Antwerp. This strategic positioning empowers ADPO to present its customers with an unparalleled and conveniently centralized “one-stop shop” logistics solution.
An important effect of the self check-in kiosk is the reduction of repetitive tasks and how it makes employees' jobs more enjoyable. This is a very interesting quality in the current war on talent.
The challenge
ADPO is a fairly complex organisation due to its diverse set of services and its multimodal setup. What is more, services were organised in reasonably independent departments with paper-based processes and little systemic integrations. Therefore, providing customers a top-notch smooth service came with its challenges.
Sub-optimal workflows
Exchange of unstructured, outdated information (phone calls, emails, paper... )
Decentralised information, despite common and shared resources
Department-specific Excels
Missing system integrations
Manual tasks and validation
Effects
Cumbersome, manual work to transfer data across systems
Errors
A challenging learning process for Juniors/Mediors
Frustration
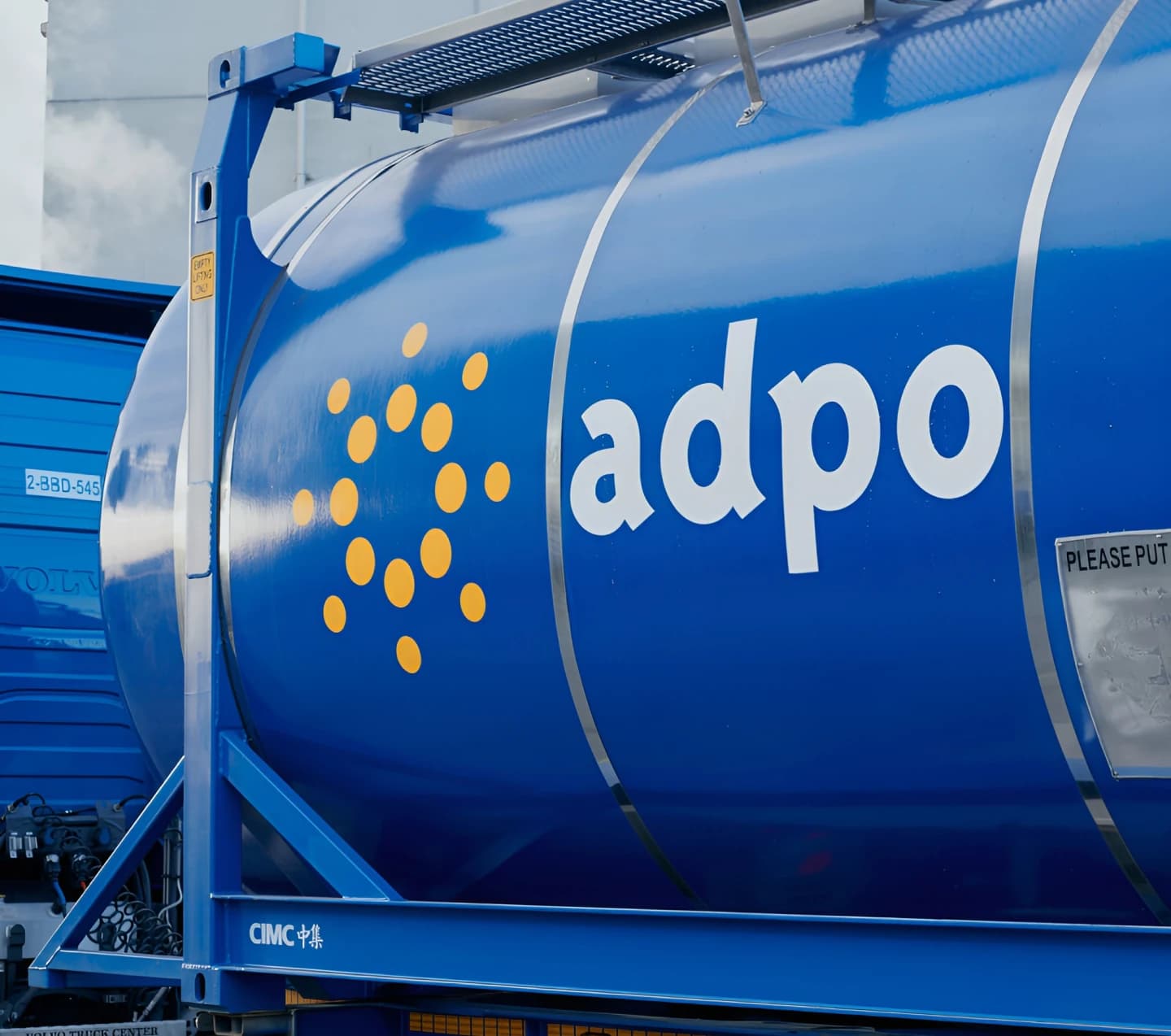
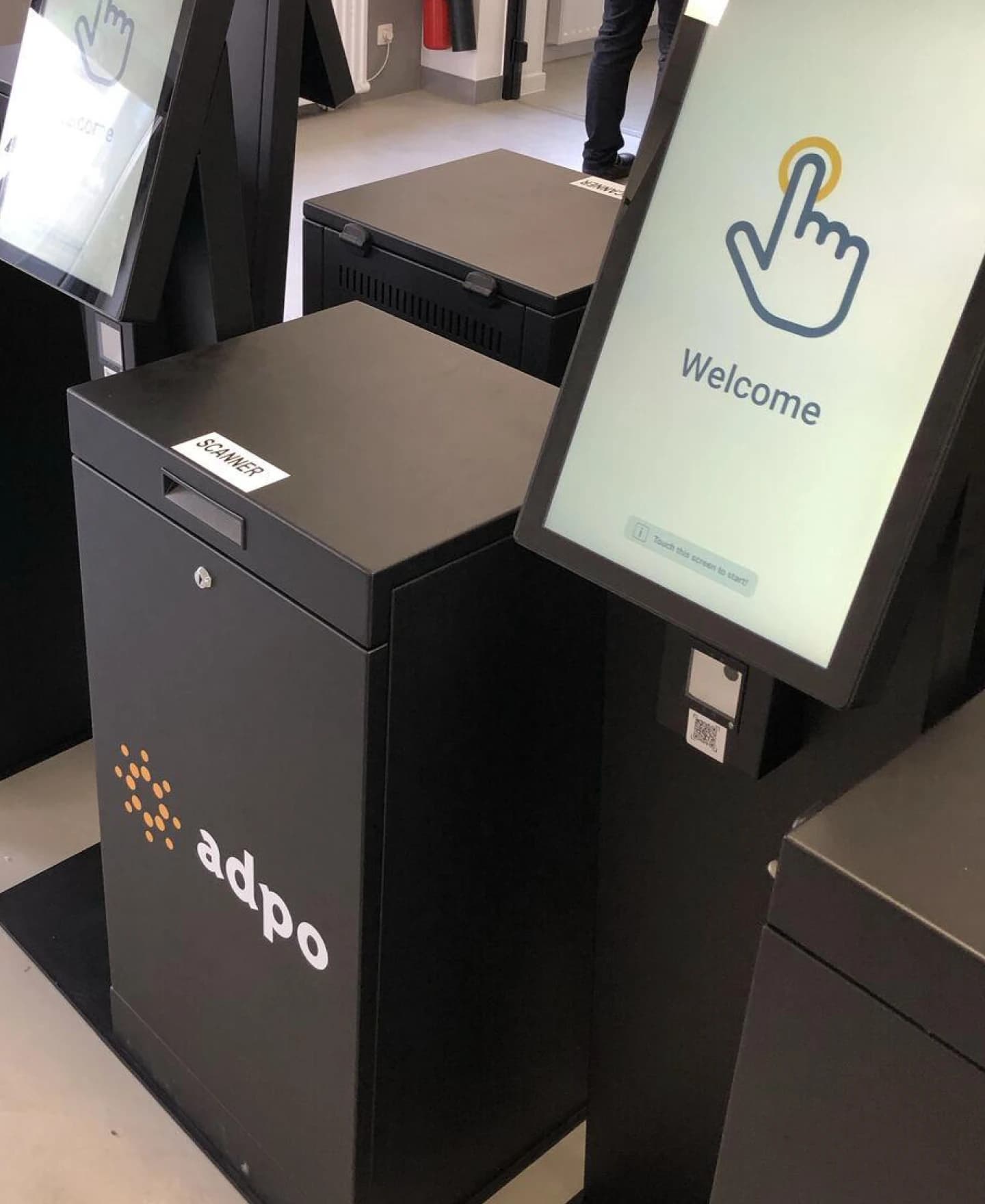
A roadmap to digitize and integrate siloed departments
For their digital transformation, ADPO found a capable partner in Made. Both partners agreed to start with an Opportunity Scan, to first identify and evaluate various areas for improvement.
Opportunity scan
The Opportunity Scan began with an Innovation Day, a full-day event to align the entire management team on the digital terminal vision. Subsequently, a series of workshops with staff and clients were conducted to gain insights into ADPO's operations, system usage, and customer interactions. Leveraging these insights, Made compiled a list of opportunities and created a digitization roadmap with clear, practical milestones.
Solution design and Delivery
After the Opportunity scan, Solution Design tracks were established to finalize the identified opportunities and translate them into development-ready designs. Following a user-centered design approach, prototypes were continuously refined and validated by end users until satisfactory blueprints emerged. The most promising designs were promptly moved into development.
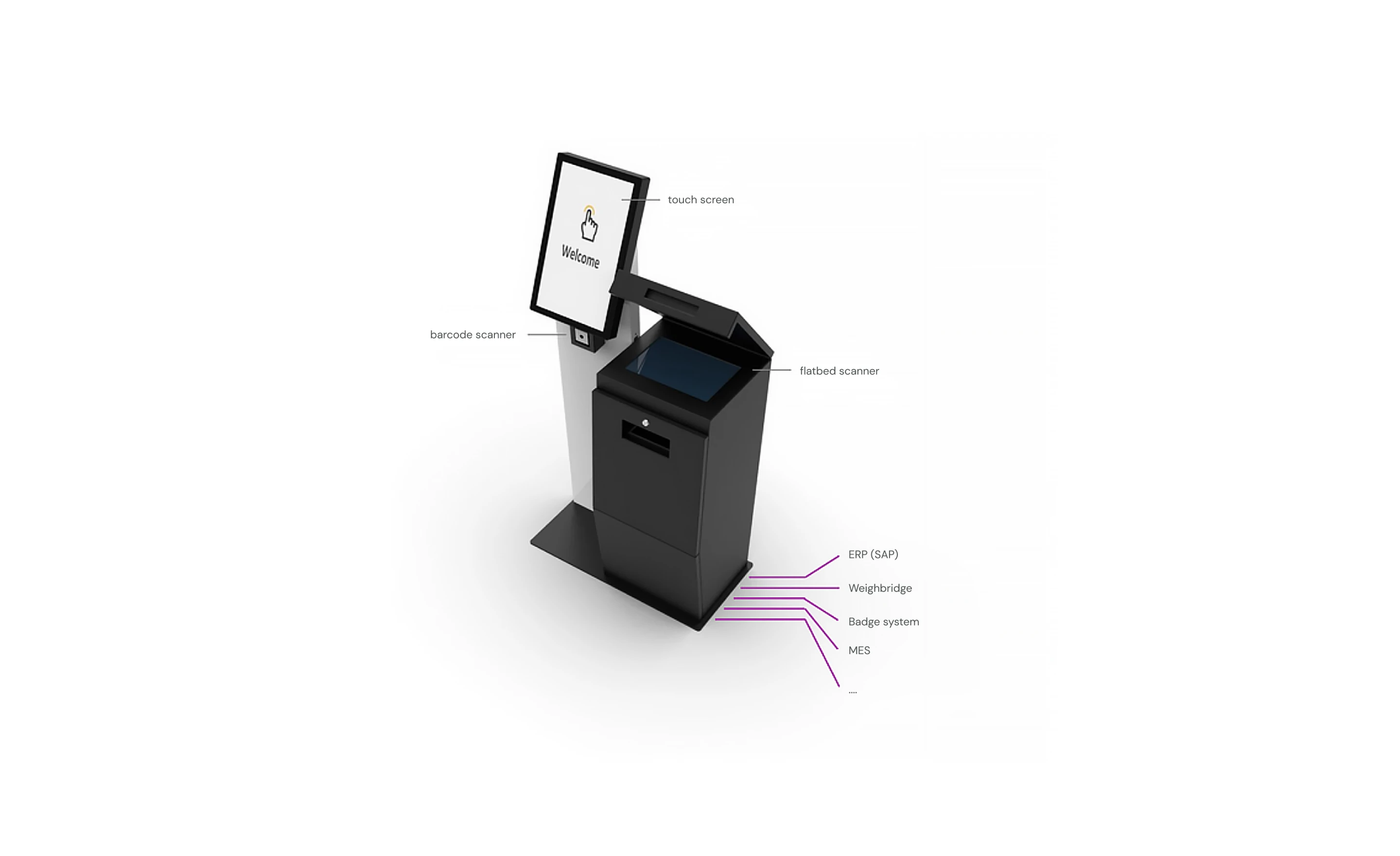
The results
Roadmap
Although the first opportunities have been addressed, the original roadmap still serves as a guide to improve operations with both technical and organisational ideas.
For example, notable initiatives ADPO implemented meanwhile are the integration of its entire front-office, the centralisation of planning, the establishment of a master data team and the update of its MES system… to name but a few.
Streamlined processes
Instead of an isolated administration based on local Excel sheets, ADPO's cleaning department now works with one intuitive application for a divers set of users: customer services, planners, operators and customers. With the implementation of the central platform, data no longer needs to be manually copied but instead, flows seamlessly through the system.
Central platform
A pivotal component to unlock all kinds of integrated services is the central platform that connects with ADPO’s previously isolated systems and interprets their data. This platform includes an integration with SAP, MES, badging and the weighbridge.
Self check-in
Highly intuitive kiosks guide +400 truck drivers per day through ADPO's registration process. The received information is transferred to the relevant systems via the central platform.
Contact
Sharing means having more, let's chat.
Ready to make your and everyone else’s future more sustainable?
Made's Industrials Innovation and Design Director Michiel Mol is keen to have a chat. Want to define what’s next together?
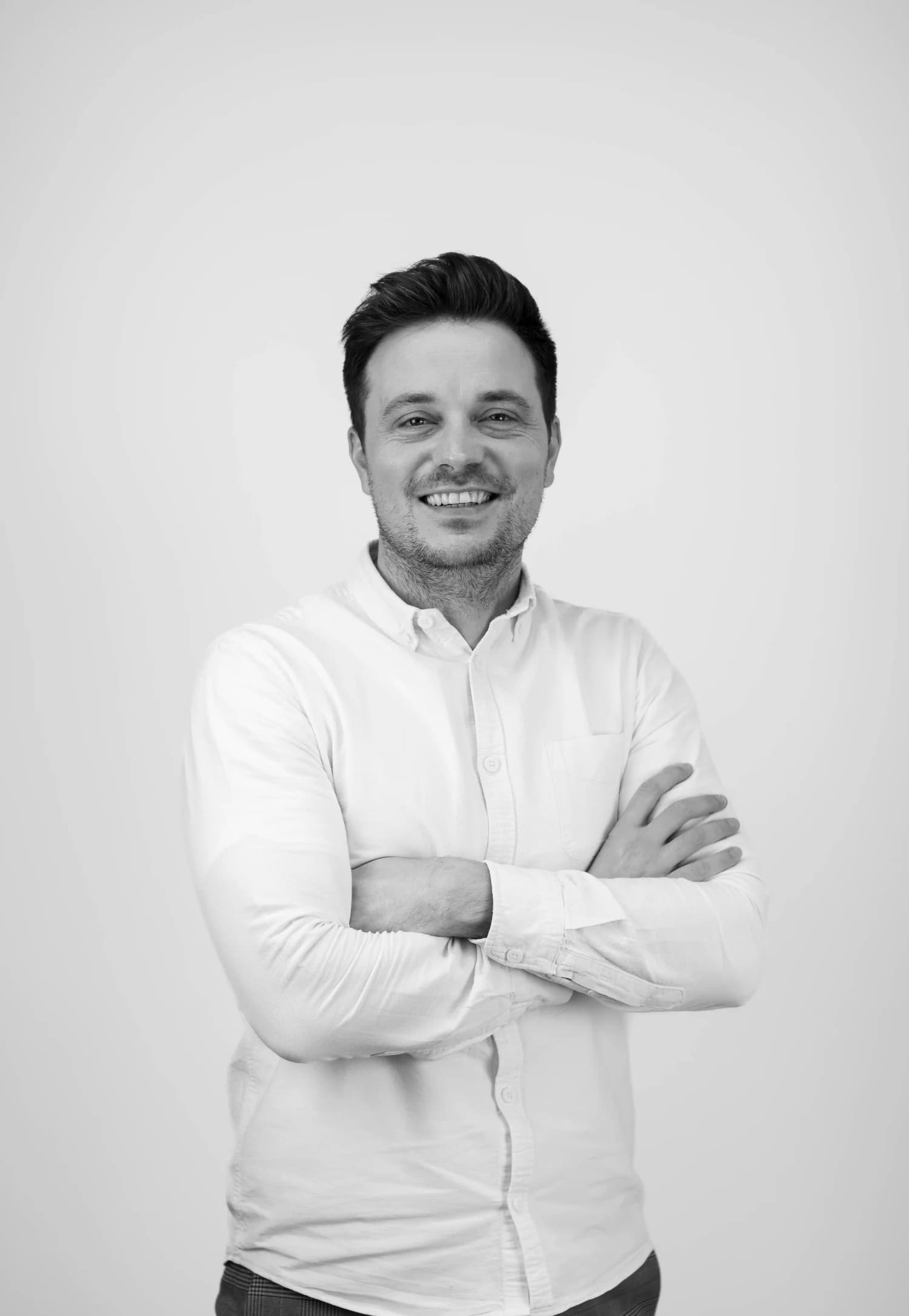